Parallel Twin Screw Barrels
Nitrided & Bimetallic for High-Performance PVC Extrusion
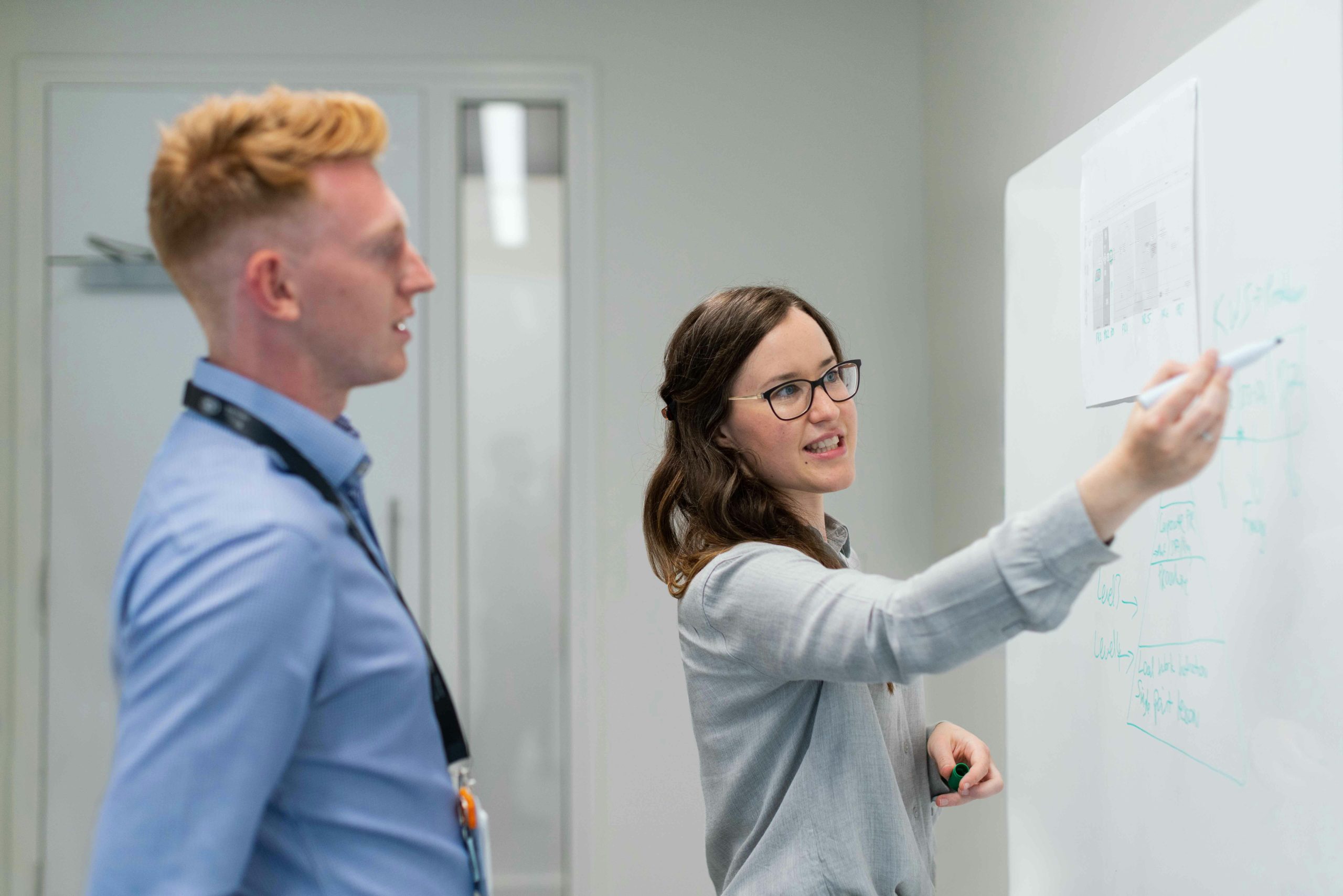
Choosing the correct barrel design is essential for achieving optimal processing performance and product quality. We evaluate material characteristics, wear and corrosion demands, temperature exposure, and required mixing performance to define the ideal geometry and metallurgical option.
- Material type: PVC, thermoplastics, rubbers, composites
- Resistance needs: abrasion, corrosion, heat
- Production targets: throughput, mixing homogeneity, torque
Our engineers collaborate with your team to create a tailored solution — from nitrided hardening to bimetallic coatings and precision machining.
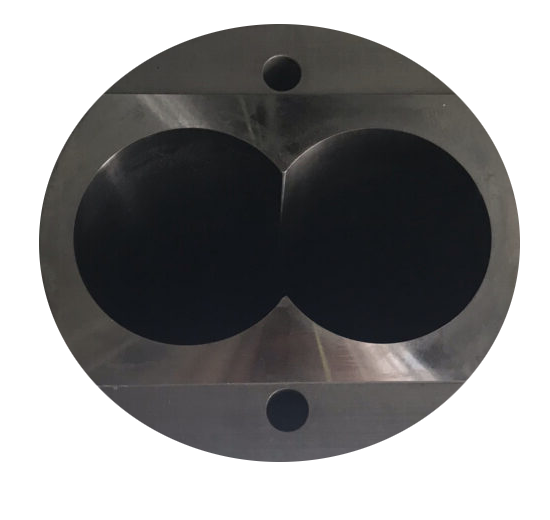
Versatile solution for general-purpose extrusion tasks. Built for steady throughput and reliable material handling across plastics and rubber processing
Both screws rotate in the same direction to provide excellent mixing and uniform melting—ideal for compounding and high-output lines.
For applications requiring higher compression and precise control. This design supports difficult formulations and high-torque processes such as PVC extrusion.
Design Options
- Customized screw geometry and compression ratios
- Variable pitch lengths for optimized throughput
- Advanced mixing section designs for better homogenization
- Precision machining for perfect meshing and high output
Advantages
- Outstanding wear and corrosion resistance
- High-performance mixing and melting
- Long operational lifespan with minimal maintenance
- Tailored solutions for specific materials and processes
Quality Assurance
- Dimensional accuracy checks
- Hardness and metallurgical testing
- Surface finish inspections
- Concentricity verification for smooth operation
Materials & Surface Treatment
- Nitrided Steel for high wear resistance and long service life
- Bimetallic Alloy for extreme abrasion and corrosion resistance
- Tool Steel Options for heavy-duty applications
- Surface treatments: nitriding, hard-chrome plating, and specialized coatings
Applications
- PVC, PE, PP, ABS, and engineering plastics
- Profile, pipe, sheet, and film extrusion
- Compounding and pelletizing
- Masterbatch production
- Recycled plastics processing
Why choose MAA Technik
Manufacturing excellence, fast delivery and custom engineering for challenging extrusion needs.
🔧 Over 20 years of experience
📐 Custom designs & prototyping
🔬 Nitrided & bimetallic solutions
📦 Fast lead times